Feng's 5E
To reduce Energy Consumption and Enhance Efficiency


I. Significance
of FCB
FCB technology is a rather complicated system technology.
It is well known that the power grid may break down due to accidents,
bad weather, war, etc. All thermal power plants are out of operation when
the power grid breaks down and cannot re-start without an external power
supply. This leads to large-scale blackouts, or power-outages. In August
2003, North America encountered a massive power failure. Then in 2012,
Hurricane Sandy hit the northeast USA, resulting in another major historical
blackout. Washington, USA and India also experienced large-scale power-outages
in 2012.
The destruction caused by a large-scale blackout is no less than that
caused by a hurricane. When a power grid collapses and cannot restore
a power supply, the resulting power failure both directly and indirectly
causes disastrous consequences.
However, units with an FCB function are able to disconnect with the grid
immediately when the power grid fails and run back to the house load operation.
This allows the unit to restore power supply to the customers and other
units in the same grid as soon as the faults are cleared, which greatly
enhances the safety of the power grid. The technology has been implemented
successfully in Shanghai WGQIII power plant.
Major features of FCB:
Recover the power grid in minutes when it breaks down, thus guarantee
the safety of power grid;
Ensure the safe and economic operation of power plants;
Minimize the consequence caused by accidents, realizing fast cut back
to house load, turbine running while generator out of operation, boiler
running while turbine trips and restarting quickly when the failures are
cleared;
Minimize the probabilities of boiler shut-down, prevent drop of oxides
and shorten the recovery time of the units.
II. Implementation
of FCB
Relative systems configuration and system design optimization:
1. Unit interlock principle------ Fast cut back; turbine run while generator
out of service; boiler run while turbine tripped;
2. Suitable configuration of bypass and reheat safety valve;
3. Suitable configuration of feed water pump, deaerator, condenser and
HP heaters;
4. Suitable operation mode and system design;
5. Suitable control strategy and electric protection.
III. Successful
Trial Operation of FCB
Waigaoqiao Phase III Power Plant has successfully implemented Feng’s FCB
technology in its two units and FCB tests from the full load performed
in March 18th, 2008 and May 21st, 2008 demonstrated the wonderful traits,
thus it becomes the unique utility in China.
The successful application of FCB ensures the safe and sufficient power
supply in Shanghai, which makes Shanghai more beautiful and bright!
Energy Saving technology
As one of the core technologies, Feng's Energy Saving Technology is based
on a deep understanding of the power plant, and takes the power plant
as a whole living system. It is a combination of series technologies and
can greatly enhance the efficiency of the power plants.
The technology has been applied in 2 ×1000MW USC Units in Shanghai Waigaoqiao
Phase III power plant and the net efficiency (with FGD and SCR) of the
units was enhanced to 46.5% from 43.5%. Here is the simple introduction:
I. Rotary Air Preheater All-round Flexible Sealing Technology
Key: Seals with controllable wearing rate are installed in the direction
of radial, axial and circle. By taking advantage of the flexibility and
contactable function, it can compensate the non-linear variation of clearance
between dynamic and static seal, realizing the all-round seal of air preheater.
Advantage: Without changing the configuration of the original equipment,
the all-round flexible seal can cover the clearance for air-leakage between
dynamic and static seal. This compensates for the deformation of rotor
and the non-linear variation of clearance. With controllable rate of wearing,
this technology performs quite reliable.
Experiment in Waigaoqiao No. 3 power plant
The air leakage rate of air preheater and power consumption for the
boiler fans are greatly reduced;
With FGD and SCR operation, the station power rate is reduced to less
than 3.5%;
The thermal efficiency of boiler is enhanced;
The efficiency of the unit is enhanced by 0.37%.
Economy: The cost can be recovered in 3 years.
II. Brand New Type and Unconventional Boiler Start Up Technology
Key: This technology changes the conventional boiler startup
method, by using steam instead of oil to heat up the boiler. The feedwater
of the startup unit can be heated up by the available steam in the power
plant, and the whole boiler then can be warmed up by the feedwater and
again by the generated steam in the evaporator. Before ignition, the boiler
has been warmed up uniformly to a certain degree and also pressurized.
When boiler fans start up, the hot air which recovered heat from the flue
gas system will be sent to the furnace and then provides better condition
for the boiler combustion.
Advantage: By taking advantage of the available steam in the power plant
to heat the boiler, the unit startup process can be accelerated. This
can save large amounts of oil and coal, which helps protect the environment.
In addition, during the heating of the boiler, its auxiliaries need not
run. Thus, the station power can be cut down. The boiler firing can be
improved significantly and its startup procedure becomes very simple and
safe. This technology can be used in all kinds of startup.
Reference in Waigaoqiao Phase III power plant:
Start-up time ≤ 2 hours( including cold start-up);
Oil consumption ≤15 tons;
Power consumption≤ 80,000kWh;
Coal consumption≤ 200 tons (include the steam used for heating).
Economy: This technology works best for new units and the investments
can be recovered during the trial operation due to many times of startup
and shutdown for commissioning. For units that are already in operation
the investment can be recovered after 5 to 8 times of boiler starts up.
III. Energy
Balanced FGD Technology
Key: A special flue gas heat recovery device is installed between
the booster fns and the FGD tower. The recovered heat is then sent back
to the turbine regeneration system for more output of the unit. Therefore,
the reduced heat rate of the turbine can offset the power consumption
of the FGD facilities. By improving the operation mode and the process,
the power consumption of FGD during the rated operation can be balanced.
Advantage: This specially developed heat recovery device is a kind of
equipment with anti-dewing, anti-corrosion and anti-blocking functions
for the heating surface. It also collects the heat generated by the ID
fan and the booster fan during their operation. Through the optimization
for the system design and the operation mode, the power consumption of
the FGD facilities is reduced to less than 0.8% during its rated operation.
Reference in Waigaoqiao Phase III power plant:
Net efficiency enhanced by 0.4%;
Water spray to the desulfurization tower reduces 45 T/h.
Economy: The cost can be recovered in 3 to 4 years.
IV. General
Application of Extraction Energy Technology
Key: By expanding from the classic regenerative cycle based on
the feedwater to general regenerative cycle on the input to the boiler
(i.e. water, air and coal, etc.), the boiler firing efficiency increased
and at the same time the turbine exhaust loss reduced.
Advantage: During unit operation, to fully take advantage of the extraction
steam in stead of the fuel, the unit total efficiency can be enhanced,
the boiler firing condition can be improved and the firing efficiency
will be better as well. During the startup of the unit, to speed up the
process of igniting and putting the coal system into operation with Feng’s
brand new startup technology, the stable firing and lower load running
of the boiler can be reached, at the same time the dewing and blockage
of the air preheater can be avoided.
Reference in Waigaoqiao Phase III power plant:
Efficiency enhanced by 0.62%;
The safe operation can be reached.
Economy: The cost can be recovered in 3 to 4 years.
Efficiency
Preservation Technology
1. Significance of SPE Prevention
With the increase of steam parameters, especially the steam temperature,
new problems and challenges are encountered, that is the steam-side oxidization
of the tubes and pipes, and subsequently SPE (steam particle erosion)
of the turbine blades, which substantially threatens the safe and economic
operation of the units. The following pictures show the destruction to
the equipment of some other power plants.
Steam-side oxidization of boiler tubes will make the heat transfer worse,
and as the tube-wall temperature rising, the oxidization will become more
serious. The oxide peeling off will decrease the flow area of the tubes.
It may even cause blockage in the tubes, which may lead to overheating
and explosion of the boiler tubes. Solid particle formed by the oxides
will also erode the turbine blades and the bypass valve plus, thus decreasing
the efficiency of the unit. While the erosion of the blades is inconvertible,
the longer the unit operates, the less efficient the turbine becomes.
SPE issues are common for the newly constructed supercritical and ultra-supercritical
units in China; overheating and explosion of boiler tubes caused by oxide
blocking occurred frequently. In the most severe cases, the unit efficiency
decreased by 8% within three years of operation.
SPE is a worldwide problem that has been disturbing the supercritical
technology field for decades. However, Feng's technologies can offer a
through solution.
2. Key Points of SPE Prevention
Inspiration from Holistic Remedy with Chinese Traditional Medicine, we
have developed a whole set of comprehensive prevention technologies for
steam side oxidation and SPE.
General Strategy:
To prevent and slow down the oxidation;
To avoid oxides from peeling off;
To blow out the dropped oxides from the boiler tubes as soon as possible
and avoid them into turbine;
To alleviate the erosion of the turbine blading by solid particles.
Prevention Technologies of SPE cover series of innovation and improvement
of units in system design, equipment selection, construction & commissioning,
control strategy, startup procedure and operation mode, etc.
3. Reference of SPE Prevention in Waigaoqiao Phase III Power plant
• SPE Prevention Tech. had been implemented successfully in two 1000MW
units of Shanghai Waigaoqiao Phase III Power Plant. After 30 months operation
of the boiler, the inspection showed that the superheater and reheater
tubes insides are smooth and as good as new. There is no any sign of oxides
hoarding and peeling off. The inspection of the turbine also indicated
that blades in the HP casing and IP casing are also as good as new. That
means the turbine efficiency kept unchanged from the first startup. No
doubt that there is no any leakage in the bypass valves.
Environment Protection technology
Feng’s environment protection includes “Energy Saving High Efficient De-dust
Technology”, “Energy Balanced FGD Technology”, “Energy Saving High Efficient
Whole Day SCR Technology” and “Safe, Energy Saving, Lifetime Extending
Technology of SCR Catalyst”, “Anti-Blocking and Anti-Corrosion Technology
for Air Preheater”.
I. Illustration of Environment Protection
1. Energy Saving High Efficient Series of De-dust Technology
The total flue gas has been greatly declined by reducing the leakage of
the air preheater, applying high efficient lower oxygen combustion technology
and improving the unit efficiency.
Modify the power supply unit of the electric precipitator by applying
high frequency power technology. Change the nominal working frequency
to the high frequency operation, and further optimize and adjust the power
supply and operation mode of the electric precipitator.
2. Energy Balanced FGD Technology
The power consumption of FGD facilities is reduced to less than 0.8% during
its rated operation by optimizing its system design and operation mode.
Applying a special heat recovery device, the heat in the flue gas and
the heat generated by the ID fan and the Booster fan during their operation
can be collected. The recovered heat can fully offset the power consumption
of the FGD facilities.
3. Energy Saving High Efficient Whole Day SCR Technology
To modify the turbine and thermal system, the extraction steam can be
increased during low load operation. This can relatively improve the feedwater
temperature in boiler low load and the flue gas temperature can be enhanced.
At the same time, to adjust the boiler heating surface, the catalyst can
run in the safe condition and high efficient area during the unit whole
load range.
4. Anti-Blocking and Anti-Corrosion Technology for Air Preheater
Expanding the philosophy of regeneration, to improve the intake air temperature
can remarkable lift the average operation temperature of the heating surface
in cold end of the air preheater. Thus the dewing area can be depressed
so that the dewing and clinging speed dropped. To ensure the flushing
by the flue gas stronger than the clinging of the attachment, the blockage
of the air preheater can be avoided. At the same time, the corrosion can
be easily solved.
5. Safe, Energy saving, Lifetime Extending Technology of SCR Catalyst
Applying Feng’s brand new startup technology, except for the advantages
mentioned in Energy Saving, catalyst poisoned, carbon and ash deposited,
and catalyst sintered, hydrates formed on its surface will be avoided.
The operation lifetime of the catalyst can be extended greatly.
Advantage:
Feng’s series of environment protection technologies cover de-dust, FGD
and SCR and can realize high efficient environment protection based on
energy saving. These technologies have predominant advantages on both
economy and environment.
II. Reference in Waigaoqiao Phase III Power Plant
The emission is greatly reduced
Emission of dust: 11mg/m3
Emission of SO2: 60mg/m3
Emission of NOx ≤ 30mg/m3
SCR efficiency≥89% (40%-100% load)
Preventing the corrosion and blockage of air preheater
Extending the lifetime of SCR catalyst
Elevated T-G unit technology
1. The Significance of Project:
Improving the coal utilization rate in the thermal power is the effective
way to reduce the flue gas pollutants and CO2 emission from their roots,
which is also the orientation of the development of high efficient clean
coal power in the world. Feng’s patent technology “a kind of cross-compound
steam turbine in a manner of high and low position arrangement” (ZL-2007-2-0069418.3)
arose at the right moment.
The research shows that adopting the above-mentioned patent technology
can greatly improve the efficiency of the unit. And the heat rate can
be decreased by 5%. Combined with the Feng’s technology innovation achievements,
which have been successfully implemented in two units of Shanghai Waogaoqiao
No.3 Power Generation Co.,LTD, the net efficiency (includes FGD and SCR)
of thermal power unit can rise to an epoch-making level of 48.92% on the
existing steam parameters 600℃ level and the circulating water temperature
20℃. Once the material for 700℃ matured, the unit net efficiency can further
go up to more than 52%.
2. The Key Technology:
Applying the patent technology “a kind of cross-compound steam turbine
in a manner of high and low position arrangement”, this advanced high
efficient ultra-supercritical power plant technology is a double reheat
unit in a cross-compound manner, where the first turbine generator train
including HP&IP1 casing is located near the boiler headers, the second
turbine generator train with IP2&LP casing and the condenser in the
conventional turbine house.
Fig
1 shows the conception design,
Fig. 1 Conception Design of Advanced High Efficient Ultra Supercritical
Plant
Through the above-mentioned design, the length of the critical piping
can be greatly shortened, that leads to the tremendous cut in the consumption
of the metallic material for the high pressure and high temperature. Meanwhile,
the pressure drop and the heat loss can be reduced enormously. Based on
this concept, double reheat which can remarkably improve the unit efficiency
while with high investment in the conventional design can be reconsidered.
3. The Project Expectation
3.1 The effect of energy saving & emission reduction
Combined this technology with Feng’s series of energy saving technologies,
the unit net efficiency can be increased at least to 48.92% (the net standard
coal consumption rate is 251 g/kWh). Thus, compared with the existing
conventional 1000MW ultra supercritical units in China, one unit can save
223000 tons of standard coal per year. It annually reduces 588000 tons
of CO2 emission, 16400 tons of SO2 emission and 164 tons of NOX emission.
3.2. Providing a basis for the development of 700℃ USC technology
700℃ advanced USC units will use a large quantity of quite expensive nickel-based
alloy material. In order to cut down the Nickel-based material to the
minimum, this compact layout would be applied in the future by 700℃ advanced
technology. Thus high temperature alloy material consumption will be greatly
reduced.
This technology provides the best solution for the design of 700℃ parameter
units under the currently feasible condition of 600℃ parameter. So it
can become a wonderful attempt and technical reserve for 700℃ USC units.
4. Evaluation
After a deep study of this technology, Siemens has given a high compliment.
Dr. Roland Fischer CEO of Siemens Fossil Power Generation stated in his
letter that “This concept with the unique chance to significantly increase
efficiency is supporting the reform of a high pollution into a low emission
green industry”, “Siemens highly appreciates this concept. We see it as
a consequent continuation of leading coal-based power plant technologies
in the world. In case this concept gets a real project, it would make
China the world’s technology leader for the steam power plants”.
FOREST POWER & ENERGY HOLDINGS,INC
Ensuring Safety---FCB (fast cut back, run back to the House
Load)
Environment Protection
Energy Saving
Efficiency Preservation
Elevated T-G unit technology
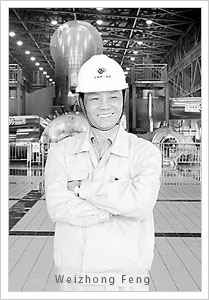